In the realm of metal fabrication, innovation has always been the driving force behind progress. One of the most significant advancements in recent years has been the widespread adoption of plasma cutters. These remarkable machines have completely transformed the way metal is cut, shaped, and fabricated. In this comprehensive article, we will delve into the world of plasma cutters, exploring their technology, applications, and the game-changing benefits they bring to the metal fabrication industry.
Table of Contents
The Genesis of Plasma Cutters
To truly appreciate the marvel of plasma cutters, it’s essential to delve into their rich history. The story of plasma cutters dates back to the mid-20th century, a time when precision cutting of metals was an emerging need, particularly for military and industrial applications.
World War II Origins
The origins of plasma cutters can be traced to the crucible of World War II. During this global conflict, there was a pressing demand for efficient methods to cut and shape metal, especially for aircraft production. Traditional methods, such as oxy-fuel cutting, had limitations in terms of precision and speed.
It was in this context that scientists and engineers began to explore the possibilities of using plasma for metal cutting. The idea was to create a superheated stream of gas that could melt through metal with unprecedented precision. This research laid the groundwork for the development of the first plasma-cutting machines.
Post-War Innovation
After World War II, the potential of plasma-cutting technology became increasingly clear. The military had witnessed its effectiveness in producing intricate aircraft components, but it was soon apparent that this innovation had applications far beyond the battlefield.
In the post-war era, industrial and manufacturing sectors began to embrace plasma cutting as a versatile and efficient method for processing metals. Early machines were large and relatively cumbersome, but they represented a significant leap forward in the world of metal fabrication.
Evolution and Refinement
As the decades passed, plasma cutters underwent significant refinements and advancements. Miniaturization of components, improvements in gas control systems, and the development of computerized controls all contributed to making plasma cutters more accessible and user-friendly.
The 1980s saw a pivotal moment in the history of plasma cutters with the introduction of numerical control systems. This allowed for precise, automated cuts and expanded the scope of applications even further.
Understanding the Technology
Plasma cutters operate on a fascinating principle: they create an electrically conductive channel of plasma through a high-velocity jet of gas. This superheated plasma can reach temperatures of up to 30,000 degrees Fahrenheit, making it a formidable cutting tool. The intense heat melts through metal like a hot knife through butter, leaving clean and precise cuts in its wake.
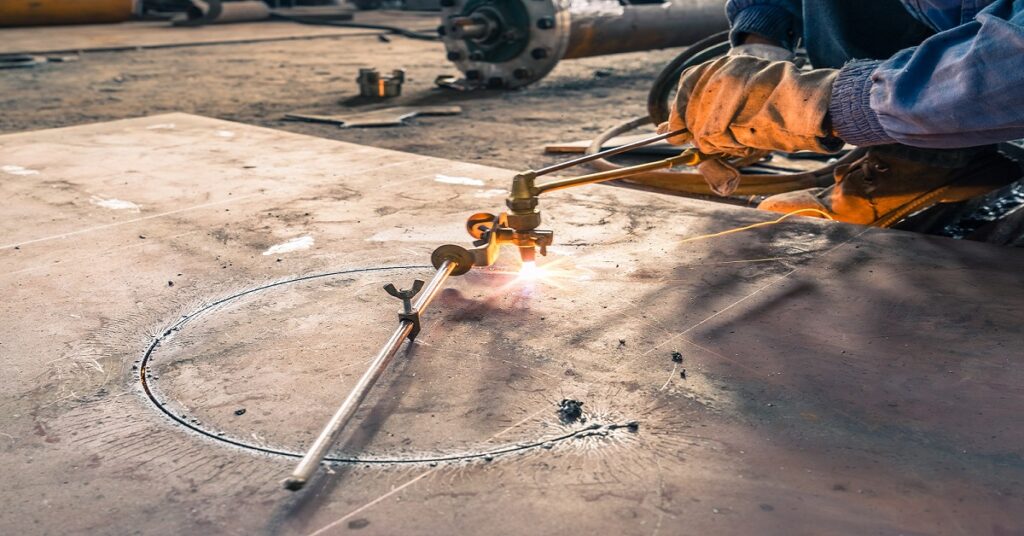
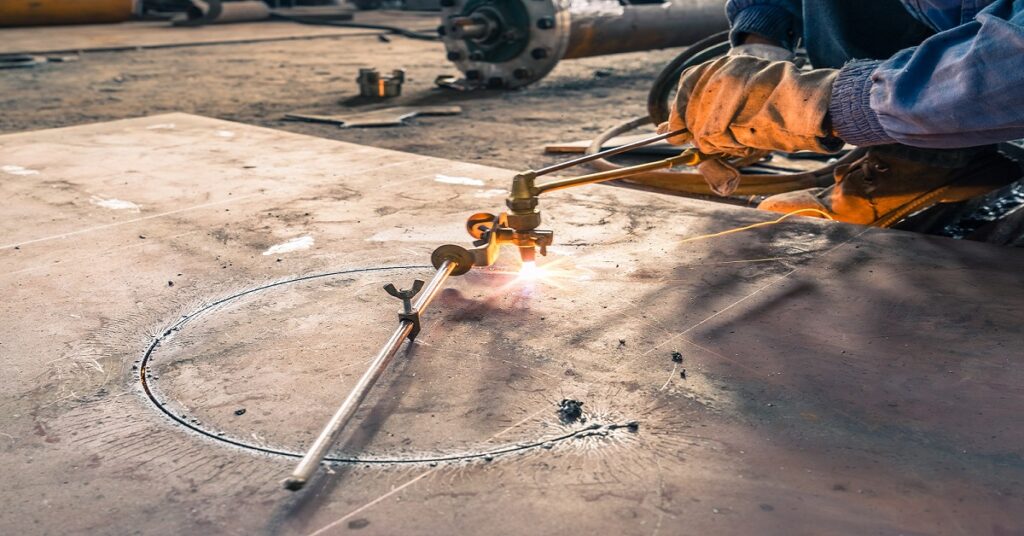
Applications Across Industries
The versatility of plasma cutters knows no bounds. They find applications across a wide range of industries, each benefiting from their unique capabilities. Here are some key sectors where plasma cutters have made a significant impact:
1. Automotive Manufacturing
In the automotive industry, precision is paramount. Plasma cutters have become indispensable for cutting sheet metal, frame components, and intricate parts with unparalleled accuracy. This not only enhances the quality of vehicles but also increases production efficiency.
2. Construction and Architecture
Architects and builders rely on plasma cutters to create intricate metal designs, decorative elements, and structural components. These machines enable the realization of complex and artistic visions in construction and architecture.
3. Metal Artistry
Metal artists have embraced plasma cutters as essential tools for their craft. The precision and speed of these machines allow artists to create intricate sculptures, metal jewelry, and customized pieces with ease.
4. Shipbuilding
In shipbuilding, where large sheets of metal must be cut and shaped precisely, plasma cutters have drastically reduced production time and waste. The result is faster construction and more cost-effective shipbuilding processes.
Advantages of Plasma Cutters
Plasma cutters offer several advantages that have solidified their position as the go-to choice for metal fabrication:
1. Precision
The high-temperature plasma jet ensures precise cuts, reducing the need for additional finishing work and minimizing material wastage.
2. Speed
Plasma cutters work swiftly, significantly increasing production rates in industries where time is of the essence.
3. Versatility
With the ability to cut through various metals, plasma cutters are versatile tools that adapt to different project requirements.
4. Clean Cuts
The clean and smooth cuts made by plasma cutters eliminate the need for extensive post-cutting cleanup, saving time and resources.
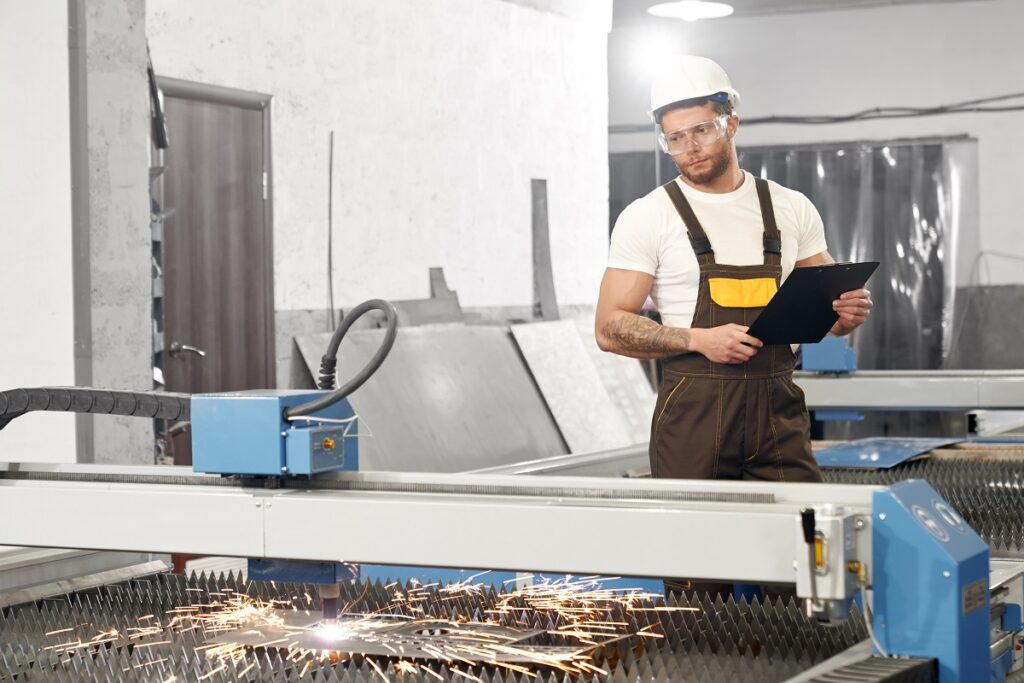
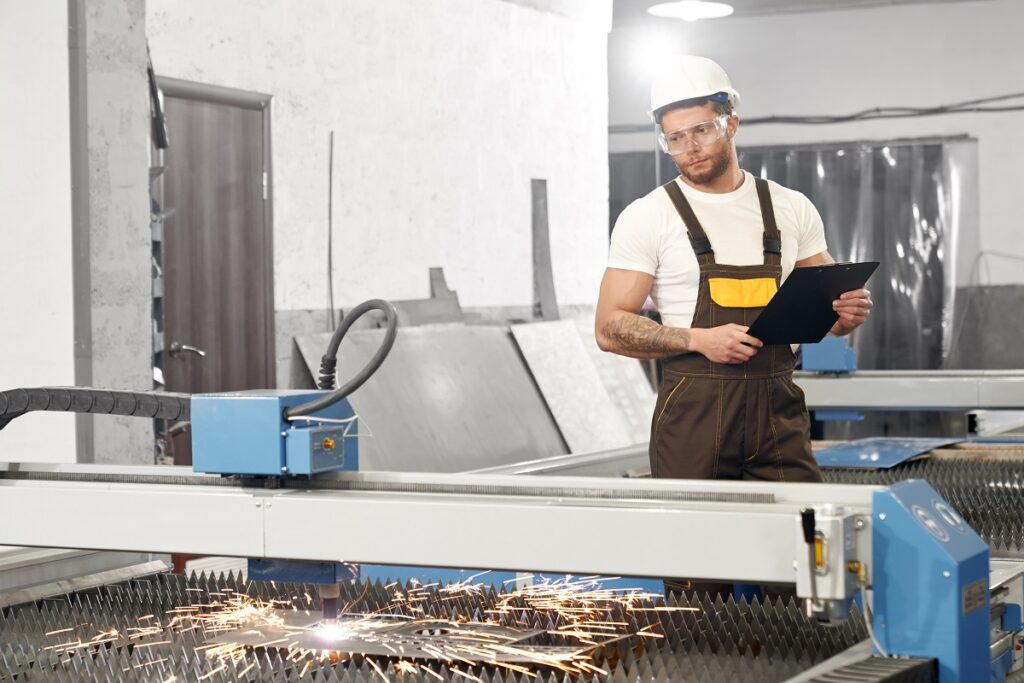
Safety and Hazards
While plasma cutters offer incredible benefits, it’s essential to address safety considerations and potential hazards. Working with such high temperatures and electrical currents can pose risks if not handled properly. Here are some key safety guidelines:
1. Protective Gear
Always wear appropriate protective gear, including a welding helmet with a proper shade, heat-resistant gloves, and flame-resistant clothing to shield yourself from the intense heat and UV radiation.
2. Ventilation
Ensure you work in a well-ventilated area or use exhaust systems to remove fumes and gases produced during the cutting process. Inhaling these emissions can be harmful.
3. Fire Safety
Have fire extinguishing equipment nearby and be prepared for potential fires. The extreme heat generated by plasma cutters can ignite surrounding materials.
4. Training
Proper training is crucial. Only trained and qualified operators should handle plasma cutters to minimize accidents and ensure the safe operation of these machines.
The Future of Metal Fabrication
As technology continues to advance, so too will plasma cutters. We can expect even more precise and efficient machines that further revolutionize the metal fabrication industry. Whether you’re in automotive manufacturing, construction, metal artistry, or shipbuilding, plasma cutters are poised to play an increasingly vital role in your processes.
Conclusion
In conclusion, plasma cutters have undeniably revolutionized metal fabrication. Their precision, speed, versatility, and ability to produce clean cuts have made them indispensable across a wide range of industries. As we look to the future, it’s clear that plasma cutters will continue to shape the world of metal fabrication, driving innovation and efficiency to new heights.